This may seem an odd title for a Blog by a H&S Consultant. However after year in the industry it is clear to us that often business owners pay for Consultant services, often as part of a combined HR Services package, because they think that they need a consultant to comply with legislation.
Yes there is a legal requirement to appoint one or more competent person to support the employer with H&S. This doesn't need to be a H&S Consultant- In small low risk businesses the owner may well have the competency to manage H&S themselves. We will return to this point later.
Every organisation must have a H&S Policy and undertake risk assessments.
When 5 or more workers are employed then these Policies and Risk Assessments must be documented.
This does not mean that small business owners are expected to be experts in H&S or indeed in Policy writing. The UK benefits from a framework based on reasonable practicability. This means that small businesses, and those in lower risk industries, do not need to have complex Management systems in place for Health and Safety.
Policies arrangements and controls are expected to be proportionate to the size and nature of the business and based on the risks of injury and ill health workers are exposed to during their time at work.
Often, I have found that those with little knowledge and experience will over complicate Health and Safety, using complex techniques and documented polices 'borrowed' from larger complex organisations. When used in smaller operations, this can result in complex bureaucracy that falls to identify the key risk to the business and its workers or can just be become irrelevant documents filed in a shelf or on a hard drive.

The Acronym K.I.S.S. ‘Keep It Simple Stupid’ or ‘Keep It Super Simple,’ is one that is relevant to this discussion. This idea dates to the mid to late 20th Century when designers US Military hardware adopted it as the rationale for their designs. The idea is that simple tools and procedures are more effective and less likely to go wrong.
In the Nuclear Industry, the Rail Industry, and other high-risk sectors there is a need for complex Risk Assessments and detailed Policies and Procedures.
However, in small offices, shops, restaurants and workshops, business owners and their workers are better served by simple and to the point processes. Complex Paperwork can become simply paperwork that is filed never reviewed and therefore lacks meaning and has no input into improving Safety and Health within an organisation.
So, what should a small business owner consider when looking at their management of Health and Safety. The Duties imposed on employers by Management of Health Safety and Welfare Regulations- Reg 7(1) requires employers to appoint one or more competent persons to assist him in meeting his legal duties. This person or persons can be internal or external. Using a Consultant H&S listed on the Occupational Safety and Health Consultants Register guarantees that your consultant:
· holds Chartered (or equivalent) status with their main professional body;
· is committed to continuing professional development;
· abides by their professional body’s code of conduct;
· will provide sensible and proportionate advice; and
· has professional indemnity insurance or equivalent to cover the nature of their duties.
Meaning that Businesses can have confidence in choosing a health and safety consultant from the register, as they are bound by their professional body’s code of conduct and are committed to providing sensible and proportionate health and safety advice.
A good Consultant will understand the business type and size and create policies and procedures that tackle the genuine issues which can differ from business to business. Many of the ‘Off the Shelf’ services will provide documentation that can often be overwhelming for the small business owner leaving them wondering how they implement the Policy and then comply with their own Policies and procedures. In effect these services may hinder rather than support the business owner.
The Health and Safety Management System
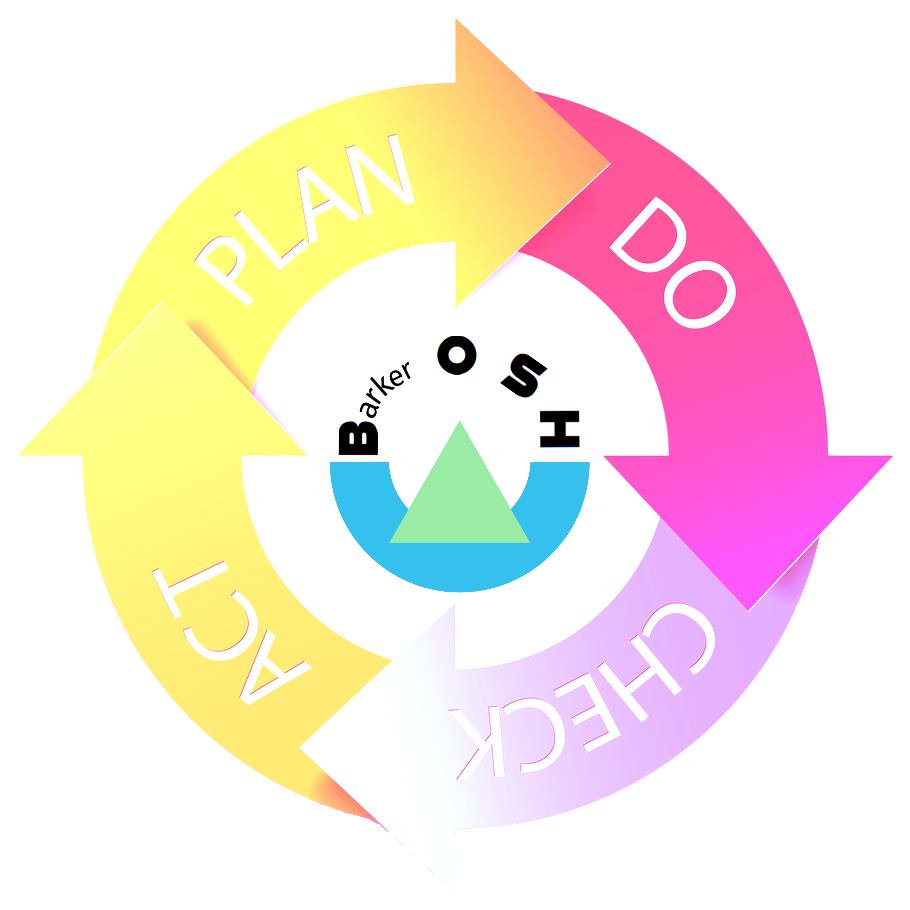
A Management System for a typical small business need not be complex or overly wordy. The PLAN DO CHECK ACT approach can sound complex if not explained correctly.
Plan
This stage is simply about having a Policy Statement outlining your overarching safety objectives and details of how these are to be achieved at a high level. This is supported by a basic Plan which details who is responsible for implementing specific actions to implement the policy and objectives.
Do
Basically, DO your Risk Assessments that identify the significant risk to Safety and Health and control measures needed to prevent harm. (See below for more on Risk Assessments)
Check
Make sure your plans are working and workers are not put at risk, Safety Inspections, Accident Investigations etc play a part but in a small business this is often just noticing noncompliant activities as they are witnessed during regular tours of the workplace or whilst working alongside the team.
Act
Ensure that the Control Measures are implemented, and Nonconformities identified during the Check process are rectified.
A good H&S Consultant can be at the centre of your Plan DO Check Act (PDCA) approach to managing H&S
Risk Assessment demystified
As discussed earlier complex businesses with complex risk can require a complex approach to Risk Assessment. However, in small low and medium risk businesses there is no need to over complicate the process. Indeed, using risk assessment tools and processes that are too complex can leave the assessor focussed on the process rather than the end goal of making the workplace safe.
So why do we do Risk Assessments- if the answer is because the law says we must then somewhere we are missing the point. There is a legal requirement to complete risk assessments to ensure the workplace is safe and that workers suffer no detriment to their Health or their Physical and Mental Wellbeing.
Furthermore, the Regulations only require that significant risk be recorded. Risks of low significance or frivolous risks need not be recorded or documented
Both the images below show paper shredders, one from a Recycling plant and one domestic type often used in small offices.


Whilst there is clearly a need for a Risk assessment of the shredder in the top image – where there is a risk to life, the one in the lower image presents little to no risk and should not under normal circumstances require a documented risk assessment.
So, what is a risk assessment? The best place to start is to explain what it is not. A risk Assessment is not a piece of Paper or a file on a computer that is looked at once every 12 months.
A true risk assessment records the collective thoughts of several people who work in, with or operate machinery within a given workplace or process. The Process is more important than the result.
There are some key definitions which can be daunting so let us explore these definitions.
Hazard
What is going to cause workers (or others) illness or injure them.
Persons at Risk
Who is likely to become ill or get injured
Existing Controls
What policies procedures, safety devices and precautions do we currently have in place to stop anyone from becoming ill or being injured.
Risk Rating
Considering the potential severity of the injury and the likelihood of it occurring is the risk High, Medium or Low. If you look at the screenshot of the HSE template they leave this step off the document, however it is a useful step to help consider next steps.
Additional Controls
What if anything can or should you do the make the task or workplace safer?
As a rule of thumb;-
Low Risk – No further Action Required- although you may wish to monitor that controls are implemented correctly
Medium Risk – Identify additional controls to lower the risk rating, these may be deemed to not be reasonably practicable in which case record the action to show it has been considered and make notes of costs and benefit to demonstrate lack of practicability. NOTE – if the potential injury or health effect is severe the cost of the control must significantly out way the benefit to safety before deeming the control to beyond the ‘reasonably practicable’ benchmark.
High Risk – STOP work until the risk can be reduce to at least a Medium Risk Rating.
Competent –
A person with the skills knowledge and experience to undertake the task, in a low-risk environment a manager is often more than capable, with some coaching, to undertake an adequate risk assessment. A consultant may help to frame the process and check that the assessor has not missed significant risk or recognised control measures.

So why do you need a H&S Consultant?
The honest answer is you probably don’t in reality need a H&S Consultant especially in office type environments.
However, in our years of experience we have seen over complex Policies and Procedures tripping up small business owners, especially when using template or example risk assessment provided by consultants that have little or no resemblance to the reality of the place of work.
For example, a risk assessment that stated Portable Appliance Testing was completed annually but the evidence to hand showed otherwise. In these situations, an incident could result in the enforcing authorities immediately taking action against the employer for not following their own procedures.
If we are engaged to offer competent H&S support as required by Reg 7 of Management of Health Safety and Welfare Regulations, we will work with you to strip away scary procedures, simplifying your management of Health and Safety allowing you to focus on the significant risk that can result in poor productive, poor moral, staff turnover, injury illness and enforcement action.
Comments